Maal means stuff.
My neighbour’s son hadn’t done his homework—when asked why, the kid replied because of supply chain issues.
Except for some dock workers who used to scream “supply chain” when they were having sex, nobody gave a shit about them up until last year. We had discussed the supply chain issues and the shipping crisis in previous issues, and not many shits were given.
But things have gotten a whole lot worse. Supply chain issues are affecting everything from toilet paper, books, solar panels, health equipment, medicines, breakfast cereal, semiconductors, chicken wings, diapers, to underwear. Basically, global trade is as resilient as all the useless shit manufactured in China—China maal!
Empty shelves are a common sight across supermarket chains. Some large chains like Walmart and Costco are even chartering their own ships to import goods. Supply chain managers are divorcing their wives and are marrying port workers, truck drivers, and shipping containers just to move goods quickly. Some newly-wed logistics managers are even calling their kids “Supply Chain” instead of “Tommy” and “Johnny.”
The phrase “supply chains” has become like a chant:
It’s a classic case of The Bullshit effect. Wait, no, that’s not right. Sorry, it’s The Bullwhip Effect. One small issue causes a giant ripple effect, and a continuous feedback loop emerges.
But these shortages aren’t all that important. I mean, if there are medicine and health equipment shortages, some people will die. Big ducking deal! Who cares? It’s good for the planet.
The biggest crisis humanity is facing because of this supply chain crisis is that we are seeing a widespread shortage of “Potty Putters.” Millions of people worldwide are sitting on potties with their pants down with nothing to do. IT’S A CRISIS!
This is causing some serious issues, and you are to blame, you despicable garbage person. YES, YOU! By sitting on your couch and ordering shit, you don’t need like medicines, food, vegetables, exercise equipment, furniture and books, you are making this supply chain crisis worse.
Just to recap, the global economy until 2019 was slowly jogging along like a long-distance runner. But then COVID came and hit the global economy right in the knees with a hockey bat. The global economy crashed as the entire world went into lockdown because some asshole thought eating a bat for breakfast was a good idea.
As the world shut down, factories too shut down because there was no demand. A lot of manufacturing capacity either went offline or was repurposed to manufacture whatever was in demand. Imports and exports crashed as people were hiding from the stupid virus. Oh, except for toilet paper, demand for pretty much everything crashed. Humanity collectively thought: “Look, this virus will kill me, but if I am dying anyway, I want my ass to have the best and most luxurious treatment possible.”
To stop the world from sinking into a depression, our friends at central banks printed money out of thin air and gave people free money. Magic! People also withdrew money from their pensions, sold stonks and were sitting on a lot of savings compared to pre-stupid virus levels.
But then we found a vaccine to murder the stupid virus, and the world quickly reopened. Then a weird thing happened. People wanted revenge for all the time they lost being locked in their homes and basements. They started revenge shopping for useless shit like food, medicines, furniture, books and electronic goods. Global trade snapped back like a rubber band. Look at the numbers. That’s a stunning recovery.
And this revenge shopping is causing a yuge supply chain crisis around the world. There are a lot of simplistic narratives about the root cause of this crisis, and often people blame it on increased demand or COVID, it’s not incorrect, but it’s entirely correct either.
This supply chain crisis isn’t caused just by one or two things. It’s a result of supply shocks, demand shocks, COVID, poor port infrastructure, a fetish for efficiency over resiliency, trader wars, labour issues, regulatory issues, politics, and just pure bad luck, all at the same time. You might have read a lot of stylized linear narratives about how A happened, which led to B, and C is the result. But you have to understand that modern supply chains are a complex maze with an insane amount of moving parts and complexity.
A port worker farting in China can lead to low sales for Walmart and DMart—it’s called the Butterfly effect, look it up. Having said that, since you’re clearly an idiot, I’m going to present a stylized and dumbed-down version of the supply chain hell the global economy is in right now.
The first thing you gotta understand is that shipping goods is not like buying software. If there’s a lot of demand for some software, the geeks can almost scale in an instant. All they have to do is press some buttons on their AWS dashboard. But importing and exporting goods requires physical infrastructure. Ocean shipping accounts for 80-90% of global trade. Over $14 trillion worth of useless crap travels on the high seas. In normal times, global shipping works fine. Here’s an illustration of major shipping routes.
Ships used to pickup cheap shit manufactured in China by kids whose first words after they were born were either “Nike” or “Gucci” and dump them in Amrikan ports such as the Los Angeles and Long Beach. On the way back, they picked up Amrikan stuff like Soy and Pork for China.
The truckers and Railways then moved the cheap Chinese shit from the ports to warehouses and inland depots. Amazon then used to deliver that shit to your house, where you took 37 minutes to get your lazy ass off the couch and collect the delivery. This system used to work perfectly fine except when there wasn’t a bloody virus trying to murder us in our sleep.
Act 1: Container shortages
But there was a stupid virus (COVID) and it disrupted the entire world. When the virus first went on a murder spree, countries went into lockdown and port operations were curtailed. So the ships that were already en-route to their destinations dumped the containers at their destination ports and didn’t pick up other containers on the way back. Shipping companies also cancelled routes given that the world was shutdown. The most severely affected route was between US and China, which is where a bulk of the demand flows.
Asia and China, in particular, was the first region to lift the lockdown. The factories in Asia were suddenly flooded with orders because of the pent-up demand from the lockdowns. The American eater was out for revenge. He was hungry and angry. Given that people weren’t going out yet, services spending also spilt over into spending on goods, leading to a sudden demand shock.
But the factories in China couldn’t ship goods because shipping containers were stuck in all the wrong ports, such as the US and Europe. On top of that, shipping goods from China to the US was way more profitable than carrying empty containers back to China. So ships started sailing back empty to China than wait for empty containers in the US, further worsening the situation. The situation got so bad that Chinese manufacturers were offering to pay a premium to get the empties back to China.
3 Chinese companies manufacture 80% of all shipping containers, and this concentration, as we discussed in the previous issue, was also a problem. Even though the production of containers is up, it still isn’t enough to ease the shortages. Again, shipping isn’t software.
Act 2: Port congestion
So the ships started picking up whatever they could and started heading to large markets like the US and Europe, where the biggest spike in demand for cheap Chinese shit was. But now, the ports were getting congested. Now, if you look closely, there isn’t a mega demand spike contrary to all the narratives as seen through port throughput and container shipping volumes.
But this was enough to overwhelm the port infrastructure around the world. Nearly 600 ships with several hundred billion dollars worth of cargo are waiting for weeks to dock and unload them at ports. Here are the worst-hit ports:
Act 3: Shipping rates
With containers in shortage and ships stuck at ports, exporters were scrambling to find containers and ships to export goods. Here’s a nice visual from Flexport on the gap between demand and supply of ocean shipping capacity:
As a result, shipping rates shot through the roof:
It was an all year Diwali for shipping companies. Maersk reported its best quarter in its 177 years of existence:
The Danish firm, which the FT has called the bellwether of international trade, reported a net profit of $2.7bn for the first three months of 2021, compared with $209m for Q1 2020.
Shipping intelligence firm Drewry is predicting an EBIT of $300 billion for shipping carriers:
Carriers will continue to make splash investments over the short and medium-term, because they can, and because they are being closely scrutinised. Drewry’s combined projected industry EBIT for 2021-22 is about $300 billion, which is an extraordinary war chest to play with, while ongoing repairs to balance sheets will make carriers less sensitive to asset value inflation or concerns about being over-exposed when the market corrects.
Here’s a chart comparing shipping rates in 2020 with 20201 for context:
Given the delays, the time taken to ship good shot up across the globe. For example, on average, it used to take 40 days to ship a Potty Putter from China to Amrika. Now it’s over 70 days. This caused further downstream effects like manufacturing slowdown, further congestion of ports, lower inventories and persistent demand.
Millions of Amrikans are making the ultimate sacrifice by just potty…ing and not putting. The global supply chain is a cruel mistress.
Act 4: Downstream effects
So why are the toilets clogged, sorry ports are clogged, you wonder? Oh, you intelligent, inquisitive person you. Shipping of goods is just one part of the story. While port congestion is grabbing all the headlines, there are far bigger issues.
Somewhere in China, a kid is born. After 2 years, the first word it says is “Nike”. The kid joins a sweatshop and starts making Nike Sneakers. The factory guy packs all the Nike shoes “not made with Child labour” and puts them on a boat. The boat comes to the port of Los Angeles, Amrika.
Now the trucks enter the scene, and they carry the containers from the port to warehouses, unload them and return the empty containers. So, now the port workers unload the container ship with Nike shoes and place the containers on truck chassis. Here’s where the first problem begins.
There’s a severe shortage of truck chassis—the metal frame attached to a truck on which containers are transported. This is again because of another downstream effect. Usually trucks carry loaded containers to warehouses, unload em and deliver the containers back to the port. But thanks to the stupid virus, there was a sustained surge of imports, which lead to warehouses being full. At the same time, there’s a severe shortage of warehouse workers due to COVID, low wages, horrendous working conditions, and little to no benefits. So chassis are stuck at warehouses for weeks. This again feeds back to the port because if there are no chassis, ships can’t be unloaded, and they are stuck at port.
Now, let’s say the trucker somehow manages to unload the non-child labour Nike shoe container and get back to the port; he isn’t able to unload the container because the port yards where containers are stored are full because of the import surge. So, chassis are stuck at ports, warehouses and streets with empty containers.
It’s one giant feedback loop!
Adding to the problem is the US-China trader war. Our favourite orange-coloured ex-president had imposed a 200%+ tariff on Chinese chassis, which made things worse and led to shortages. And then, there’s the fact that the chassis market is fundamentally broken due to years of underinvestment, shortage of mechanics, and other structural issues:
The roads the trucks drive on are crumbling—one freight forwarder said they lose half a dozen chassis a week to the deep potholes outside the ports. According to the Pool of Pools, which aggregates information from the marine chassis operators of the Ports of Long Beach and Los Angeles, of the port’s 58,000 chassis, 2,158 (pdf) are currently broken, and the specialized mechanics who fix them are likewise in short supply.
The other problem is there is an issue with the availability of truck drivers, particularly in the US. There isn’t a shortage, as headlines depict. The problem is that the annual turnover rate of truck drivers is 94%. So, the truck companies have to replace all their drivers every year. That’s because trucking is a brutal job. Drivers have to spend long hours on the road away from families, and the pay is horrible, all thanks to the deregulation of trucking in the 1970s. On top of that, mental and physical health issues are rampant.
At the same time, their pay has sunk. In the late 1970s, driver salaries were up to 50% higher than they are today, even when accounting for inflation, according to Wayne State University economics professor Michael Belzer.
In the US, the median salary for the 1.9 million truck drivers stands at $45,260. Nearly 40% lack health-insurance coverage, compared to 17% of the working population.
On top of that, most truck drivers are independent contractors and are paid by the mile, which means they don’t get paid for the time they spend waiting at ports etc. Apart from their driving duties, they are also forced to do a lot of other things like loading/unloading, training etc., for which they don’t get paid.
This quote about the plight of truck drivers is telling. Truck wages is for most parts, an inhumane wage arbitrage:
“The port truck driver, for decades now, has basically been the slack adjuster in the whole system,” said Steve Viscelli, an economic sociologist with the University of Pennsylvania who studies labor markets and supply chains. The entire system, he said, is built around free labor from truck drivers as they wait for containers.

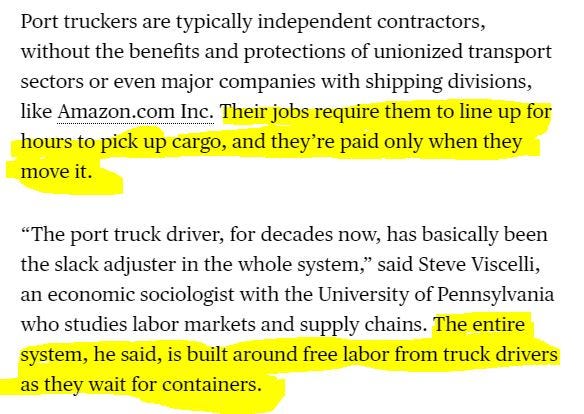
And then, to finally round it all up, the port infrastructure is still stuck in the dark ages. From a shortage of workers and equipment to software systems that run on Windows 2000 BC, port infra sucks. This finally feeds back into the system in the form of more delays. Drivers who could do multiple loads a day now are lucky if they do one.
It’s not just the trucks. Railways are another essential cog in moving cargo from ports to inland depots. Even railways are struggling with the same issues—shortage of labour, chassis and space to store containers. As a result, cargo volumes have been wobbling while railway operators are seeing increased revenues on the back high freight rates, just like the shippers.
The odd thing, and adding to the earlier point, is that the spike in container volumes isn’t a huge one compared to the pre-stupid virus period. If such a moderate spike can cause port and shipping infrastructure to crumble, shit gonna be hard, yo!
ACT 5: Give it to me, baby, now!
All these supply chains and shipping issues have led to a pretty loud debate about efficiency vs resiliency. Globally, since the 80s, companies have adopted something called “just in time (JIT)” or “lean manufacturing” practices. Toyota first figured this shit out in the 50s and 60s. At the risk of sounding reductive, the idea was to eliminate inefficiencies in manufacturing, thereby improving efficiency and, by extension, profitability.
The just-in-time (JIT) inventory system is a management strategy that aligns raw-material orders from suppliers directly with production schedules. Companies employ this inventory strategy to increase efficiency and decrease waste by receiving goods only as they need them for the production process, which reduces inventory costs. This method requires producers to forecast demand accurately. - Investopedia
So over a period of time, companies built complex supply chains spanning the entire globe in search of the cheapest manufacturing and labour. Naturally, all roads led to China, which became the world’s factory and also the world’s biggest chokepoint. As the saying goes, “When China sneezes, the world catches a cold”.
The whole argument is that JIT works well in normal times since companies have some visibility over demand and can order raw materials and intermediate goods to match the production levels. But when poop 💩 hits the fan like a stupid virus and there are supply and demand shocks, just in time becomes poop and doesn’t work. So the “experts” say that companies hence shouldn’t just singularly focus on efficiency but also resiliency. This means higher inventory, reducing the geographical concentration of suppliers, vertical integration and so on.
But I think a lot of nuance is lost in this debate. For all the shit just-in-time gets, it’s one big reason why we have all the cheap goods we don’t need. If companies build inventories, onshore manufacturing, and shipping companies, ports and railways build slack by adding some idle capacity, there are costs, which will inevitably be passed back to consumers. Similarly, there are labor, political, economic, and environmental considerations. It’s easy to forget the tremendous environmental damage we’ve exported by relying on China and feeling good at home.
It’s no surprise that others want a crystal ball of their own. Just-in-time supply chains are nearly dead. The disruptions of the past two years sank many businesses that chased hyper-efficiency to an extreme. Warehouse space is expensive, and paying to store inventory you might not need for a week can seem extravagant in times of plenty. But when next week’s stock doesn’t show up, you have nothing to sell.
“Before the pandemic, most companies were focusing on cutting costs,” says Simchi-Levi. Now they’re willing to pay for resiliency, but focusing on resiliency alone is also a mistake: you need to find the right balance between the two. This is the real power of simulations. “We’re seeing a growing number of companies starting to stress-test their supply chains using digital twins,” he says. - MIT Technology Review
ACT 6: Inflation
Since 2008, the hawks across much of the developed world were predicting that all the money printing by the central banks would unleash hyperinflation reminiscent of the Weimar Republic. But inflation never arrived, it stayed stubbornly and persistently low due to a lot of structural reaons like globalization, demographics, and technlogoy.
But inflation finally is here, and supply chain disruptions are partly responsible.
There are two camps to this debate. One camp believes we are entering an era of persistently high inflation rates. The other camp believes that these inflation spikes are transitory and caused largely due to supply chain issues and high energy prices. This is a loud and contentious debate, one that I am not nearly qualified to comment on, nor do I want to. Making predictions is a bit like astrology, and I am no astrologer, although it’s a nice scam to make good money. But the fact remains, we have inflation today, and we already see companies hike prices.
Some select good reads.
Do you people even click on these? Be honest. Don’t lie. Tell me in the comments!
Investing & markets
Voodoo economics
Crypto
Playlist
Too many interesting podcasts to catch up on this week. Here are a few interesting ones on my playlist:
This article presents shit as shit needs to be presented. The efforts of collecting data , reading articles takes a lot of time and effort. Kudos to you
Great place for knowledge, humour and sarcasm.